Schwingungen an rotierenden Maschinen werden mit Sensoren erfasst. Eine nachgeschaltete Auswertungselektronik überwacht diese Signale und alarmiert bei Grenzwertüberschreitungen. Ziel der Schwingungsüberwachung und des Maschinenschutz ist es unzulässige Schwingungen zu erkennen, und Ausfälle zu vermeiden.
Je nach Maschinentyp empfehlen sich unterschiedliche Systeme und Konzepte. Unabhängig davon, ob Sie eine Wälzlager-, Gleitlager- oder Unwucht Überwachung für Motoren, Lüfter oder Pumpen benötigen: Vom smarten Schwingungssensor bis zu skalierbaren, vielkanaligen Maschinenüberwachungen beraten wir Sie passgenau und liefern komplette Lösungen vom Sensor bis in die Cloud.
Wir beraten Sie bei der Auswahl einer geeigneten Lösung.
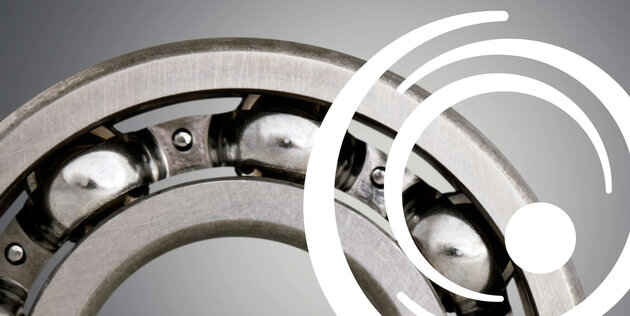
Wozu wird ein AVIBIAline Gerät eingesetzt?
Die AVIBIAline-Serie ist für die Maschinen-Schwingungsüberwachung mit kombinierten Funktionen zur Wälzlagerdiagnose nach DIN 3832 entwickelt worden. Die Geräte sind zur Verwendung mit Standard IEPE Beschleunigungssensoren konzipiert. Je nach Konfiguration wird die Beschleunigung zur Schwinggeschwindigkeit oder dem Schwingweg integriert und überwacht. Breitbandkennwerte können genauso überwacht werden wie Ordnungskennwerte.
In einer alternativen Konfiguration können Stossimpulskennwerte zur Lagerschadensdiagnose berechnet und ebenfalls überwacht werden. Verändern sich an einer Maschine gerade diese Kennwerte rapide, ist eine sehr schnelle Abschaltung notwendig um Schäden zu minimieren. AVIBIAline Geräte sind mit 2 oder 4 Eingangskanälen lieferbar. Jedem Analogeingang ist ein Analogausgang zur Anbindung einer SPS zugeordnet. Darüber hinaus sind Alarmausgänge als Relais- oder Digitalausgang verfügbar. Die Konfiguration der Geräte ist Offline oder Online über USB möglich. Die AVIBIAline X Serie ermöglicht es Rohsignale oder Kennwerte über die LAN-Schnittstelle zu übertragen.
- Modulares und kostengünstiges System zur Maschinen-Schwingungs-Überwachung nach ISO 10816
- 2 oder 4 kanalige Ausführungen sorgen für eine optimale Skalierbarkeit
- Einfache Konfiguration über USB-Schnittstelle, Überwachung der Zonengrenzwerte nach Norm
- Erweiterte Möglichkeiten zur Stossimpulsdetektion und Wälzlagerzustandsbeurteilung
- Schnelle Digitalausgänge und zusätzlich Monitoring Ausgänge als 4..20mA Schnittstelle
Einsatzgebiete von AVIBIAline sind Pumpen, Ventilatoren, Lüfter, Elektromotore, rotierende Maschinen mit Wälzlagern.
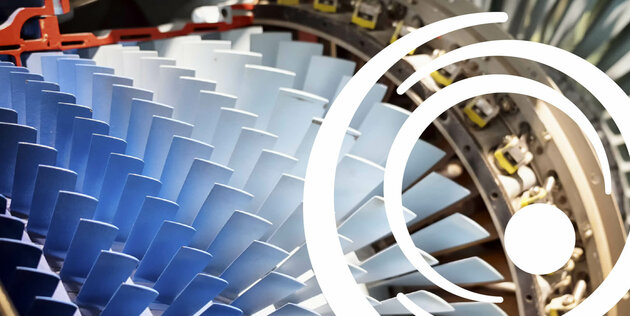
Wozu wird ein PMM-300PLUS Gerät eingesetzt?
PMM-300PLUS ist ein kompaktes Schwingungsüberwachungs- und Analysegerät. PMM-300PLUS besteht aus 4-kanaligen Erfassungsmodulen die autark arbeiten.
- Modulares und kostengünstiges System, autarke Einzelgeräte
- Wellenschwingung, Lagerschwingung, Wickelkopfschwingung
- Interner Datenspeicher zur Erfassung des hochaufgelösten Zeitsignals im Störungsfall
- Optionale Anbindung an die Schwingungsanalysesoftware ORCA
Die PMM-300PLUS Serie besteht jeweils aus 4-kanaligen Erfassungsmodulen für unterschiedliche Anwendungen, die es erlauben eine verteilte Architektur aufzubauen. Die Ankopplung eines Analyse-PCs oder einer SPS-Steuerung erfolgt über die integrierte LAN-Schnittstelle. PMM-300PLUS erfasst und überwacht absolute Lager- und relative Wellenschwingung an Turbinen oder Generatoren nach DIN 10816. Jedes PMM-300PLUS Gerät kann die Drehzahl erfassen und eine Untersuchung harmonischer Schwingungsanteile und dazugehöriger Kennwerte ausführen.
Die synchronen, dynamischen Eingänge sind zum Anschluss von IEPE-Beschleunigungssensoren als auch von Wellenschwingungssensoren oder beliebigen dynamischen Sensoren geeignet. Das PMM-300PLUS kann über analoge und digitale Ausgänge einfach an ein Automatisierungssystem angeschlossen werden. Für die Analyse von Rohsignalen befinden sich „Buffered Outputs", ausgeführt als BNC-Buchsen, auf der Gerätefront. Zusätzlich stellt jedes PMM-300PLUS Erfassungsmodul die Messwerte und Kanalstati über Modbus (RTU und TCP) zur Verfügung. Tiefergehende schwingungstechnische Analyse wie FFT, Orbit und Wasserfalldiagramme sind mit der optional lieferbaren Orca Analysesoftware möglich.
Einsatzgebiete für PMM-300PLUS sind Pumpen, Ventilatoren, Lüfter, Elektromotore, Generatoren und größerer rotierende Maschinen.
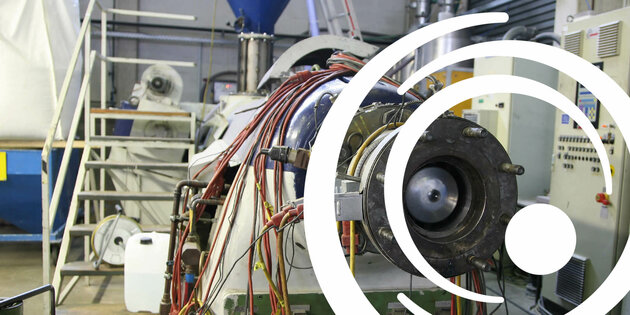
Wie funktioniert ein smarter Schwingungsschalter?
AVVS-Schwingungsschalter erfassen die Beschleunigung und integrieren diese zur Schwinggeschwindigkeit oder berechnen direkt im Sensor eine FFT-Analyse. Mittels einer frei parametrierbaren Hüllkurve können erlaubte Schwingungszustände definiert und Online überwacht werden. Die Konfiguration erfolgt über USB-Schnittstelle oder einfach durch eine Teach-In Funktion.
- Überwachung von Schwingbeschleunigung und -geschwindigkeit
- 60 Frequenzbereiche von 0,1 bis 10 000 Hz für Effektiv- und Spitzenwert programmierbar
- Signalisierung von Vor- und Hauptalarm über blinkende LEDs
- Einfachste Inbetriebnahme: 1. Installieren, 2. Teach-in drücken, 3. überwachen
Die Schwingungsschalter der Reihe AVVS ermöglichen die Grenzwertüberwachung von Effektiv- und Spitzenwerten mit wählbaren Grenzfrequenzen. Zum Schalten externer Lasten dient ein Relaisausgang. Mit den Geräten AVVS11 und AVVS12 ist auch eine Überwachung im Frequenzbereich möglich. Dazu wird das Frequenzspektrum der Beschleunigung gebildet und in zehn frei wählbaren Frequenzbereichen mit Grenzwerten verglichen. Beim AVVS12 wird der USB-Anschluss über eine Buchse nach außen geführt. Er eignet sich somit zum direkten Anschluss an Computer für schnelle und einfache Schwingungsmessungen. Die Geräte enthalten piezoelektrische Beschleunigungsaufnehmer, wodurch hohe Präzision und Auflösung sowie ein breiter Frequenzbereich erreicht werden.
Einsatzgebiete von smarten Schwingungstransmittern sind die Zustandsüberwachung an Motoren, Lüftergebläsen, Pumpen, Kompressoren etc. nach DIN/ISO 10816, eine smarte Qualitätskontrolle in der Produktion mit frequenzselektiver Überwachung, die Notabschaltung an Produktionsanlagen, bei denen Vibrationen zu Gefährdungen führen können, Schwingungsüberwachung an Schienenfahrzeugen und Sicherheitsschalter an Türen und Toren.
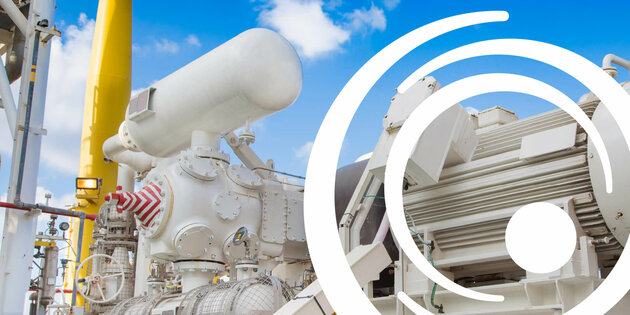
Wie funktioniert ein Schwingungstransmitter?
Schwingungstransmitter erfassen die Schwingstärke an rotierenden Maschinen und liefern einen 4...20 mA Stromschleifensignal analog zum Effektivwert der Schwinggeschwindigkeit. Das Normsignal kann direkt an standardisierte MSR-Technik, wie Grenzwertrelais oder eine SPS angeschlossen werden. Als Besonderheit besitzen manche Transmitter einen Selbsttesteingang, bei dem das interne Sensorelement angeregt und somit der gesamte Transmitter getestet werden kann. Mit dieser Zusatzfunktion kann in regelmäßigen Abständen automatisiert geprüft werden, ob der gesamte Loop vom Sensor bis zur Überwachung einwandfrei arbeitet.
- permanente Überwachung der Schwingstärke an rotierenden Maschinen nach DIN/ISO 10816
- 4...20mA Stromschleifensignal analog zum Effektivwert der Schwinggeschwindigkeit
- Selbsttestfunktion zur automatisierten Validierung der gesamten Messkette
- Elektrischer Anschluss erfolgt über M12 Anschlussstecker
- direkter Anschluss an standardisierte MSR-Technik, wie Grenzwertrelais, SPS, etc.
Schwingungstransmitter werden eingesetzt um eine Unwucht-Überwachung an: Ventilatoren, Pumpen, Kompressoren, Zentrifugen, Lüfter, Gebläse, Rüttler, Dekanter, Separatoren, Antriebe, Getriebe, Mischer, Förder- und Transporteinrichtungen zu realisieren.
FAQs für den Bereich Schwingungsüberwachung und Condition Monitoring
Der Begriff Unwucht im Zusammenhang mit rotierenden Maschinen oder Apparaten beschreibt die Auswirkungen von drehzahlfrequenten Schwingungsanteilen, verursacht durch ungleiche, verschobene Massenverhältnisse und dadurch generierte ungleiche Fliehkräfte. Unwucht wird auch als drehzahlharmonische Schwingung oder Schwingungsamplitude der ersten Ordnung bezeichnet.
Um eine Vorstellung zu bekommen wie ein Unwucht entsteht und sich anfühlt, kann folgendes Beispiel heran gezogen werden. Räder müssen am Auto regelmäßig ausgewuchtet werden. Insbesondere dann wenn auf eine Felge ein neuer Reifen aufgezogen wird. Nach dem Auswuchten der Räder fährt das Auto gleichmäßig und das Lenkrad zittert nicht. Fährt der oder die Fahrer:in dann zu schnell durch ein Schlagloch oder eine Bordsteinkante, kann es zu kleinsten Verformungen an der Felge kommen. Dadurch werden die Massenverhältnisse an der Rad-Reifenbination geändert und die Ursache für eine Unwucht ist geschaffen. Das resultierende Problem erledigt sich nicht mehr von allein. Der Fahrer bemerkt die Unwucht durch ein einem Zittern, oder schlimmer noch durch ein „Schlagen“ am Lenkrad.
Es ist möglich, dass die an der Felge entstandene Unwucht das Lenkrad nur bei bestimmten Geschwindigkeiten zum Zittern oder Schlagen anregt. Die Ursache dafür ist, dass die Unwucht die Eigenfrequenz eines anderen Bauteils anregt und dieses in Resonanz bringt, was im schlimmsten Fall zu ernsthaften Schäden führen kann. Dieses Beispiel gilt natürlich nur für Fahrzeige die noch über ein mechanische Verbindung (= Lenkradsäule) zwischen Rädern und Lenkung verfügen. Bei modernen Fahrzeugen mit Steering by Wire ist der Effekt so nicht mehr reproduzierbar.
Wie oben beschrieben können sich Unwuchten auf andere Maschinenteile fortpflanzen und diese zu Schwingungen mit großen Amplituden anregen. Der resultierende Effekt nennt sich Resonanz und kann zu desaströsen Auswirkungen führen. Deshalb ist es wichtig Unwuchten zu überwachen und zu hohe Unwuchten zu beseitigen. Um das Beispiel vom Lenkrad auf eine Industriemaschine zu übertragen: Gleiche Effekte entstehen bei Industrieventilatoren wenn es durch das transportierte Medium durch den Lüfter zu Anbackungen an den Ventilatorschaufeln kommt und diese die Massenverhältnisse verschieben und so Unwuchten auslösen.
Die Messung der Unwucht (Drehzahl Harmonische Schwingung) ist sehr wichtig für die Maschinenüberwachung und gleichermaßen für die Zustandserfassung. Erfahrungsgemäß ist die Unwucht die Ursache Numero uno für hohe oder schädigende Maschinenschwingungen. Es gibt viele Ursachen für eine Unwucht:
- Lose Bauteile auf den rotierenden Wellen
- wärmebedingte Unwuchten durch Geometrieänderungen
- Anbackungen von Material an Schaufeln, Lüfterrädern, …
- Abbrüche oder Abschleifungen
- zu großes Lagerspiel
- Verschiebungen im Magnetfluss zwischen Rotor und Stator
Die Unwucht wird auch als Schwingstärke bezeichnet und in der Einheit der Schwinggeschwindigkeit mm/s gemessen.
Die Unwucht kann mit unterschiedlichen Messsystemen und Sensorlösungen erfasst und überwacht werden. Zunächst ist es wichtig zu verstehen, dass die Schwinggeschwindigkeit (Einheit in mm/s) proportional zur Schwingungsenergie ist und somit den richtigen Parameter für die Überwachung darstellt.
Im Bereich der Schwingungsmessung sind folgende drei physikalische Größen von Bedeutung:
- Schwingbeschleunigung (Einheit: g oder m/s²)
- Schwinggeschwindigkeit (mm/s)
- Schwingweg (µm oder mm)
Die drei Messwerte können durch Integration oder Differentiation ineinander überführt werden. Allerdings gilt das nicht beliebig in jede Richtung und ohne Einschränkungen.
Da Beschleunigungssensoren deutlich preiswerter als Schwinggeschwindigkeitssensoren sind, werden diese in den meisten Fällen für die Maschinenüberwachung eingesetzt. Die Schwingbeschleunigung kann durch einfache Integration in die Schwinggeschwindigkeit umgerechnet werden.
Ein Sensor mit entsprechender integrierter Elektronik wird als Schwingungstransmitter oder einfach nur als Transmitter bezeichnet. Transmitter berechnen die Schwinggeschwindigkeit in einem vordefinierten Frequenzbereich und geben den Messwert (die Unwucht) als 4..20mA Signal aus. Demnach stellen Transmitter die einfachste Lösung dar die Unwucht zu überwachen.
Allerdings muss etwas wichtiges beachtet werden: Ein Transmitter berechnet die Schwinggeschwindigkeit in einem bestimmten Frequenzbereich. Typisch - und nach Norm - von 10Hz bis 1000Hz. Die untere Grenze von 10Hz bedeutet- übersetzt in Drehzahl - 600 U/min. Unterhalb dieser Drehzahl ist der Transmitter quasi „blind“. Treten die Unwuchten unterhalb dieser Grenzfrequenz auf, könnte die Maschine auseinanderfliegen und der Transmitter würde weiterhin nur einen sehr kleinen Messwert liefern und keinen Alarm erzeugen. Wie man sieht, ist es sinnvoll sich bei der Auswahl einer Transmitterlösung gut beraten zu lassen.
Eine weitere Möglichkeit der Unwuchtüberwachung ist der Einsatz von Beschleunigungssensoren die ab etwa einer Frequenz von 1,5Hz .. 3Hz messbare Pegel produzieren. Die Signal des Beschleunigungssensors werden zu einer externen Elektronik übertragen, die einer Signalfilterung (in einstellbaren Frequenzbereichen) durchführt und die Integration zur Schwinggeschwindigkeit( = Schwingstärke = Unwucht) übernimmt. Der Messwert wird als 4..20mA Signal oder über eine Feldbusschnittstelle ausgibt.
Besonders langsam laufende Maschinen, wie zum Beispiel Wasserkraftmaschinen die mit z.B. 120 U/min drehen, können nicht mit Beschleunigungssensoren auf Unwucht überwacht werden. In solchen Fällen werden deutlich teurere aber ausschließlich geeignete elektrodynamische Schwinggeschwindigkeitssensoren eingesetzt. Diese Art von Sensoren erzeugen bereits bei kleinsten Drehzahlen ab etwa 1Hz (=60 U/min) bereits gut messbare Ausgangspegel. Vorteil diese Sensoren ist zudem, dass keine weitere Integration erforderlich ist, weil das Ausgangssignal der Sensoren direkt den Messwert in mm/s ausgibt. Typische Sensorempfindlichkeiten sind hier 100mV/mm/s.
Diese Frage kommt sehr häufig bei der Parametrierung von Überwachungssystemen auf. Das Maß der zulässigen Unwucht kann über verschiedene Maßnahmen ermittelt werden. Die Norm DIN 10816 gibt Hinweise darauf. Dort werden Maschinen nach Maschinentyp, Leistungsklasse und Fundamentgestaltung angegeben. Diese Norm unterscheidet die Maschinenzustände A, B, C, und D, wobei „A“ den Optimalzustand und „D“ den Gefahrenbereich mit dringend empfohlener Abschaltung definiert.
Dennoch fällt es immer wieder schwer die zu überwachende Maschine den in der Norm beschriebenen Klassen zuzuordnen. Was dann? Es ist zu empfehlen den Hersteller der jeweiligen Maschine zu kontaktieren und nach den erlaubten Schwingungspegeln befragen.
Was, aber wenn diesbezüglich keine Informationen zu bekommen sind? Dann ist der Anlagenbetreiber in die Aufgabe versetzt Grenzwerte festzulegen oder Schwingungsexperten zu beauftragen die Einstellungen vorzunehmen. Dabei müssen Fragestellungen wie die folgenden geklärt werden? Läuft die Maschine aktuell „ruhig“ oder steht eine Wartung unmittelbar bevor? Gibt es ggf. weitere Maschinen gleicher Bauart deren Schwingungspegel miteinander verglichen werden können?
Die Überwachung der Unwucht ist für den Maschinenschutz essentiell, aber nur ein eingeschränkter Indikator für eine wartungsorientierte oder vorausschauende Instandhaltung. Ist eine hohe Unwucht vorhanden, muss schnell gehandelt werden.
Der Lagerzustand eines Wälzlagers kann mittels Unwucht Messung nur unzureichend beurteilet werden. Im Sinne einer vorbeugenden oder zumindest wartungsorientierten Instandhaltung müssen weitere Indikatoren untersucht werden, um einen sich anbahnenden Lagerschaden zu erkennen bevor es zu einer gravierenden Unwucht kommt.
Solche Indikatoren sind Wälzlagerkennwerte wie BCC, Sturmzahl, Crest Faktor und weitere. Darüber hinaus gehen analytische Verfahren wie das Hüllkurvenfrequenzspektrum mit Lagerschadensdatenbank.
Die DIN 3821 beschreibt die Wälzlagerzustandsbeurteilung mittels Wälzlagerkennwerten. Wälzlagerkennwerte helfen – durch Analyse Ihres Trendverlaufs – zu erkennen, ob ein Lager geschädigt ist und ob es sich verschlechtert. Kennwerte werden mit Beschleunigungssensoren erfasst und die Messignale auf periodische Stöße untersucht. Stöße entstehen zum Beispiel, wenn Wälzkörper über geschädigte Lagerschalen rollen und dabei „Klackgeräusche“ (= Stöße) erzeugen.
Mit dieser Methode ist eine Einschätzung des Lagergesundheitszustands möglich. In DIN 3832 werden verschiedene Methoden beschrieben Wälzlager mit Kennwerten aus dem Zeitbereich zu überwachen. Z.B. bezogener Effektivwert, bezogener Spitzenwert, k(t) Zahl, Crest, BCU,… Wichtig ist zu wissen, dass es oft nicht reicht nur den aktuellen Wälzlagerkennwert zu messen. Vielmehr muss hier der Trend im Auge behalten werden. Der absolute Zahlenwert eines Wälzlagerkennwertes ist oft nicht aussagekräftig, zumal die Condition Monitoring Systeme in bestehende Anlagen, mit einem vom Neuzustand abweichenden Schwingungsverhalten, eingesetzt werden.
Natürlich wäre es optimal direkt vom Neuzustand einer Maschine einen Wälzlagerkennwert aufzuzeichnen. Aber in der Praxis ist das nicht immer der Fall. Das CMS wird in einem unbestimmten Zustand installiert. Umso wichtiger ist in solchen Fällen die Trendentwicklung. Schäden verursachen im Zeitsignalverlauf eines Lagerschadenskennwertes oft exponentielle Anstiege. Daher werden Wälzlagerkennwerte oft in logarithmischer Darstellung aufgetragen.
Wälzlager lassen sich mit breitbandig aufgenommenen Kennwerten überwachen. Wenn sich im Wälzlager ein Defekt anbahnt, wie z.B. eine Beschädigung der Lauffläche im Außenring (Pitting), so erfährt jeder Wälzkörper beim Durchlaufen dieses Defektes einen Stoß und erzeugt ein breites Anregungsband in der Umgebung des Lagers. Aufgrund dieses sehr breiten Anregungsbandes treten z.B. Eigenfrequenzen von benachbarten Bauteilen hervor oder die Eigenfrequenz des Sensors selbst wird angeregt.
Da sich Lagerschäden zumeist in Amplituden im hohen Frequenzbereich darstellen, wird als Messgröße die Schwingbeschleunigung in m/s² verwendet. Kennwerte auf einem breiten Frequenzband erfassen diese, durch die Lagerschäden verursachte, Überhöhung. Dabei wird vorrangig der Frequenzbereich von 1000 Hz aufwärts betrachtet, um drehzahlproportionale Anteile (wie zum Beispiel die Unwucht) zu unterdrücken.
Für Wälzlagerkennwerte bedeuten höhere Amplituden ein höheres Ausmaß der Schäden im Wälzlager. So kann festgestellt werden, ob ein Schaden vorliegt. Die in AVIBIAline implementierten Wälzlagerkennwerte werden als bezogene Kennwerte betrachtet. D.h. der aktuelle Messwert wird immer mit einem Initial- oder Bezugswert verglichen.
Der Initialwert korrespondiert mit dem ungeschädigten Zustand des Lagers. Der eigentliche Messwert stellt eine einheitenlose Abweichung vom Bezugswert dar. Dieses Vorgehen ist insofern nützlich, da Kennwerte von Lagern sehr unterschiedlich sein können und daher zur Gut-/Schlechtbewertung immer der Gutzustand bekannt sein muss (Initialwert).
Die Berechnung eines Hüllkurvenfrequenzspektrums beantwortet die Frage welche Komponenten im Lager welche Schäden aufweisen. Die Komponenten des Lagers werden einzeln bewertet. Mit dieser Methode ist eine Einschätzung der Lagergesundheitszustands sehr detailliert möglich.
Eine tiefgehende Analyse des Gesundheitszustands eines Lagers und Bewertung der einzelnen Lagerkomponenten: Innenring, Außenring, Käfig und Wälzkörper wird erst mit der Berechnung des Hüllkurvenfrequenzspektrum möglich.
- Hüllkurvenspektrum als präzises Verfahren zur Ermittlung des Lagerzustands
- Messung mit Beschleunigungssensoren
- Auswertung der Rohsignale mittels signaltechnischer Weiterverarbeitung zur Hüllkurve
- Zuordnung der Schadenssymptomfrequenzen zu der Hüllkurve mittels Lagerschadensdatenbank
Eine wichtige Methode Wälzlagerschäden zu klassifizieren ist die Hüllkurvenanalyse. Sie ist ein unverzichtbares Werkzeug, wenn komplexe Wälzlagerungen vorliegen, also die Anregungen aus verschiedenen Lagern stammen und/oder weitere Körperschallquellen vorhanden sind (z.B. Getriebe).
Ziel der Hüllkurvenanalyse ist es eine Signatur der schadhaften Lagerkomponenten zu erhalten. Dies geschieht durch Sichtbarmachung der durch Schäden verursachten Stoßimpulse. Ein intaktes Lager erzeugt eine breitbandige Schwingung, treten Defekte im Lager auf so wird diese gleichmäßige Schwingung durch die auftretenden periodischen Stöße amplitudenmoduliert.
Das Verfahren der Hüllkurvenanalyse bewirkt eine Demodulation, welche die Stoßwiederholfolge (Schadensfrequenzen) extrahiert. Eine Hüllkurvenanalyse wird meist wie folgt durchgeführt
- „Herausfilterung“ von Störsignalen durch Hochpass
- Gleichrichtung des verbleibenden Signals
- Tiefpassfilterung = Demodulation der Schadenssymptomfrequenzen
- Durchführung einer Fouriertransformation
Die so gefundenen Schadenssymptomfrequenzen lassen sich Bauteilfrequenzen zuordnen und ermöglichen über Beurteilung Ihrer Amplitude und Seitenbänder eine Diagnose des Schadens, sowie des Schadensausmaßes.
Schadenssymptomfrequenzen ergeben sich durch den mechanischen Aufbau eines Lagers und können mittels der Lagergeometrie berechnet werden. Viel komfortabler ist es allerdings, wenn in der Auswertungssoftware eine Lagerschadensdatenbank integriert ist. In der Lagerschadensdatenbank geben Hersteller die von Ihnen berechneten Lagerschadenssymptomfrequenzen für Ihre Lager an. Somit kann der Anwender einfach seine Lagernummer auswählen und die Symptomfrequenzen in der Auswertung für sein Lager einblenden und deren Amplitude ablesen. Viele Avibia Analysesystem wie der AVIBeamer oder das drahtlose System AV560 und das mobile System VE 100 beinhalten automatisch eine Lagerschadensdatenbank.
In einigen Fällen reichen die hier bislang beschriebenen Verfahren nicht aus, um die Ursachen von Schwingungsproblemen zu finden und zu überwachen. In solchen Fällen werden weitere Messwerte und Anlagenparameter erfasst und zusammenhängend mit den Schwingungen analysiert. Erst die Korrelation von mehreren Einflussfaktoren liefert dann einen aussagekräftigen Wert, der überwacht werden kann. Dafür erforderlich sind Methoden der intelligenten Signalanalyse = KI erforderlich.
Mit Hilfe von KI-Methoden ist es zusätzlich möglich Optimierungspotenziale in Maschinen aufzudecken, Qualitätsprobleme zu analysieren oder auch den Wirkungsgrad der Maschine zu steigern. Das System CONDInet KI von Avibia bietet genau für diese Aufgabenstellung eine Lösung.
Hinter den KI Korrelationsverfahren stecken aufwändige und berechnungsintensive Algorithmen. Insbesondere wenn die Anzahl der Eingangsgrößen hoch ist, reicht ein PC nicht mehr aus um die Daten zu verarbeiten und die Berechnung muss in die Cloud verschoben werden.
Namhafte Cloud-Plattformen wie die von der ai-omatics solutions GmbH bieten längst Möglichkeiten an die Messwerte – auch Schwingungsmesswerte – statistisch zu analysieren. Die notwendigen Auswertungsmethoden, Regeln und Algorithmen werden von Data Analysten erstellt und in die Cloud-Systeme integriert. Ist der Einsatz cloud-basierter Systeme geplant, muss darauf geachtet werden, dass die Schwingungsmesstechnik über geeignete IIoT-Schnittstellen verfügt. OPC UA ist eines der Standardprotokolle, das zur Kommunikation zwischen Feldgeräten und der Cloud verwendet werden kann.
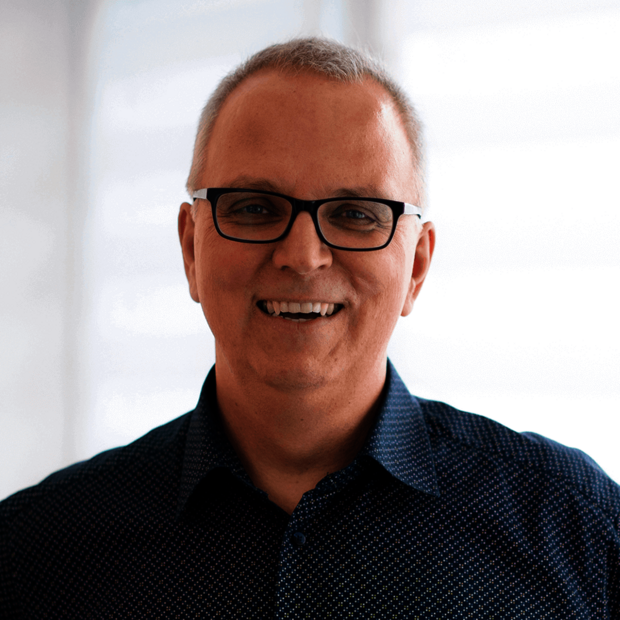
Sie möchten mehr erfahren?
Gerne. Vereinbaren Sie Ihren persönlichen Beratungstermin mit Frank Ringsdorf.